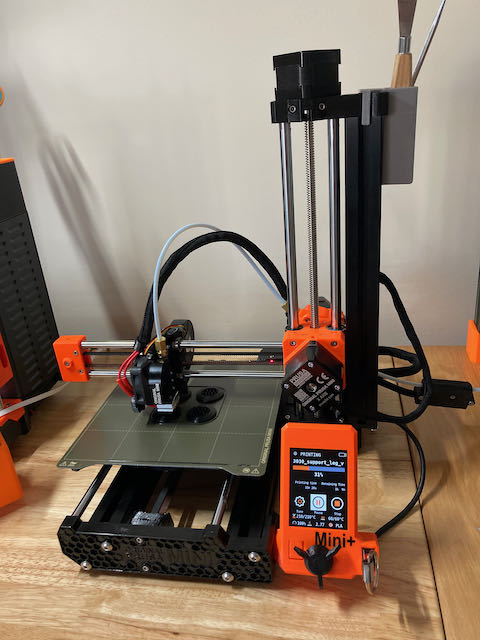
Prusa Mini+ Kit
First of all I have to say I have been 3D printing since 2015 and bought my first Prusa in maybe 2016 or 2017. So I’ve been around the block a time or two. No, I’m not a super expert like some folks but I do have some experience that lends me to share a thought or two.
My Prusa experience kind of shakes out like this:
- Bought i3 Mk2
- Upgraded i3 Mk2 to Mk2S
- Bought i3 Mk3S+
- Upgraded i3 Mk2S to i3 Mk2.5S
- Bought and built Mini + kit.
Okay, I have no huge print farm, just three printers and 5 builds and upgrades. But let me tell you this……..The Prusa Mini + is IMPRESSIVE.
You expect a lot from an $800 3D printer like the i3 Mk3S+……. that’s a no-brainer………but you don’t expect as much from a $349 3D printer.
But there’s the rub…….The Prusa Mini+ is a CRAZY GOOD 3D PRINTER. I can’t believe it. Not a lot impresses me but this printer is incredible.
Okay, what are the downsides? Number 1 it isn’t called a “Mini” without a reason. The build plate is much smaller than the other offerings. That being said there have been very few times I have stretched the limit of the size of my 3D printer bed. Most of the things I print will fit on the Mini build plate.
So let’s get down to it. After building and using the Prusa Mini+ here’s my summation statement: It prints BETTER than the other printers I own. That is saying A LOT. My other printers produce phenomenal quality but the Mini is just a hair better. The first thing I printed was a Benchy and it was the best Benchy I ever printed with anything. How is this possible with a $349 printer? My simplified answer is that it is the new controller board and stepper motors, but do read on, please!
My opinion is that the Mini+ is some kind of interim printer that incorporates the newest technology in 3D printing that hasn’t quite made it to the i3 Mk2 or Mk3 line3 yet.
The Mini+ is a radical departure from the current line up. The biggest difference could be the extruder which is now a Bowden extruder. Also it has cantilever design which means it is only supported one one side.
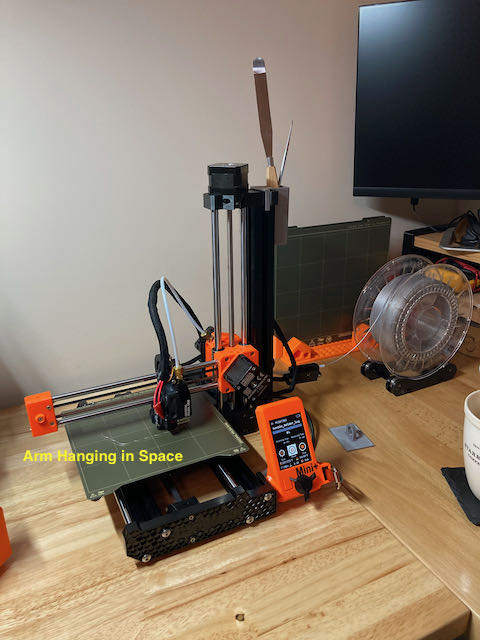
Unique design of X axis
Also it has a color LCD screen that is greatly improved over the last offerings.
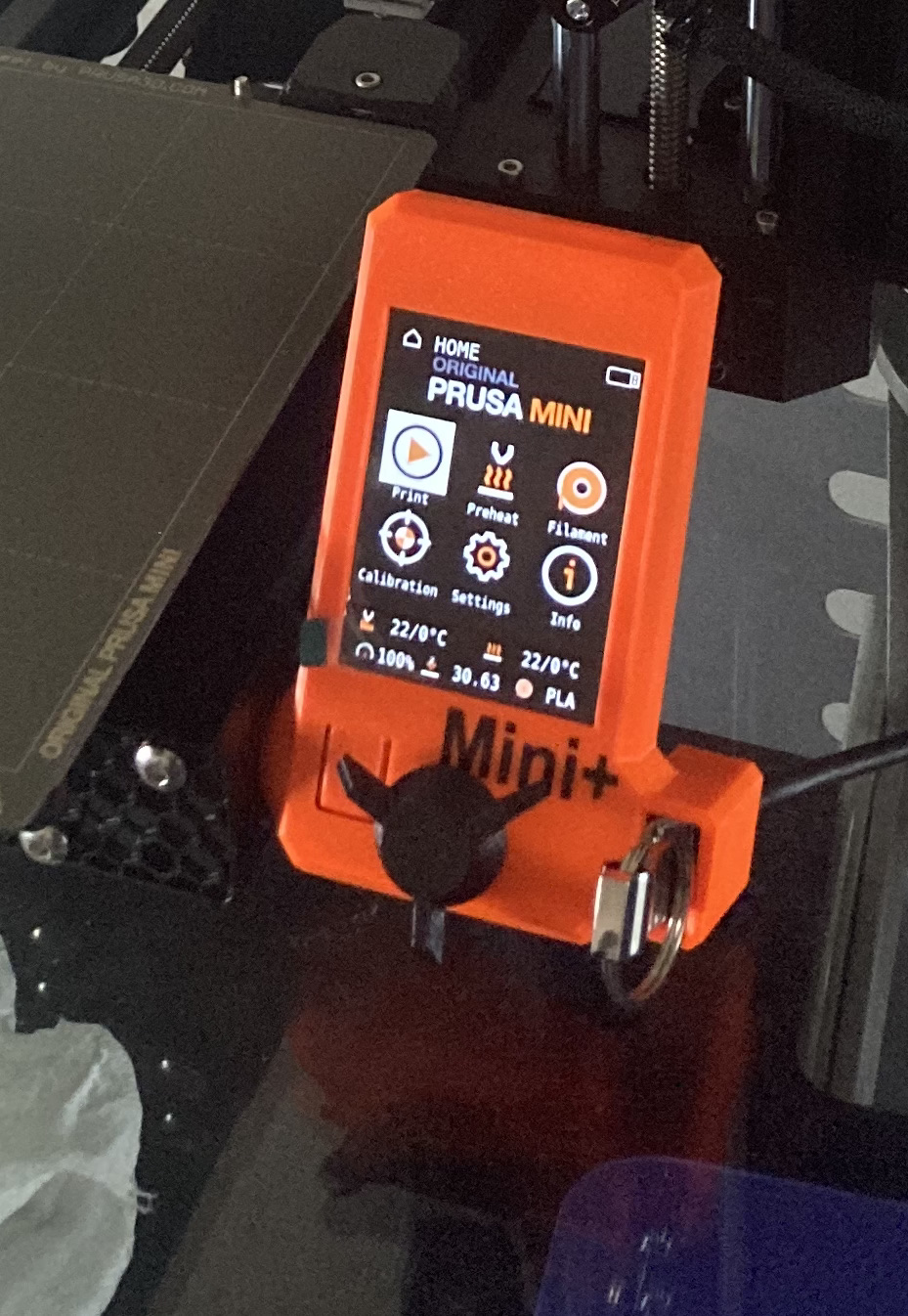
Mini+ LCD Screen
Other improvements include a 3030 aluminum base and injection molded plastic, rather than 3D printed front and back base parts. Wow, do they look so much more polished. Fit and finish is exceptional giving you a square X and Y axis right out of the chute. The controller board or “Buddy Board” is a STM32 which is a 32 bit controller which allows for more precise movements. The bearings are improved as well as the bearing clips. All this provides for better and smoother motion which results in better print quality.
The hotend is new and seems to be a custom hotend from Prusa. That is also a departure from the norm as hotends from E3D usually rule the roost. All I know for sure is my hotend works GREAT and I don’t care where it comes from.
Also the kits have evolved. Every one gets better. The instructions are better, the build quality of the included parts is better, and the logical sequence of building is improved.
And again they have added improvements not available in the other printers. The Mini has an RJ-45 ethernet jack. The current firmware includes software that can monitor BUT NOT CONTROL the print. That is a feature coming soon we are told. Also you could upgrade the firmware over LAN which is cool. There is the possibility of future inclusion of a wifi chip that can be added to the Buddy Board. I bought the chips but just waiting for the firmware to mature to that point.
So again, it looks like they took all of their great ideas for top of the line printers and stuffed them in to the Mini+
Now, on to some issues I had during the build and post build. Not a lot, but worth mentioning. When attaching the LCD to the frame they tell you to use an M3 x 20 screw and tell you it might be tight.
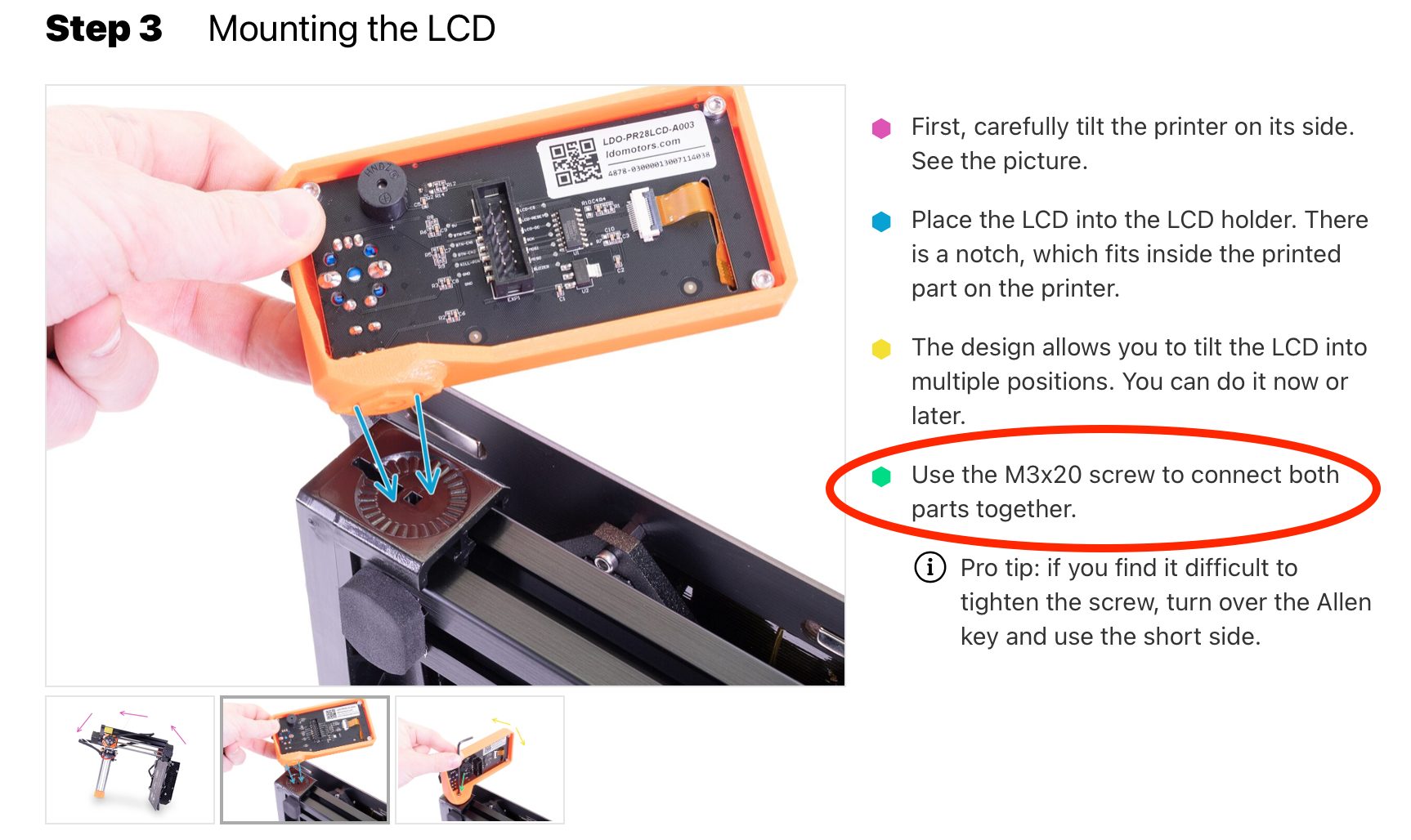
LCD mounting instructions
They clearly screwed the pooch on this instruction. I ended up using an M3 x 12 screw. I tried running the tight 20mm screw in and got it jammed and stripped the head leaving me STUCK. It was still so long I managed to get a pair of needle nose pliers under the LCD and grabbed the screw and gave it a mighty counter clockwise turn which freed it up for removal. No harm, no foul but clearly an M3 x 20 is too long here.
The next issue I had was post build. My printer failed the setup wizard for the heat bed test. When I ran down the error it spit out on line it said on their web site that the heat bed test would fail unless the steel sheet was placed on the bed. This is NOT in the Preflight Checklist.
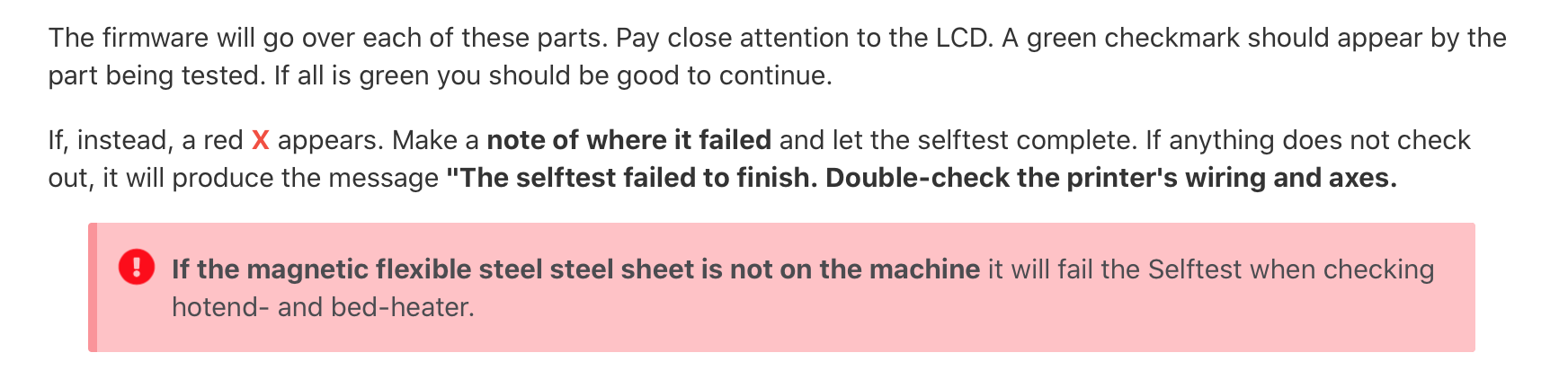
Mini Self Test Caution
Then when I tried to do a First Layer calibration, instead of doing a 16 point mesh bed leveling it stopped after the first row on test point number 4. I hopped on Support chat with Prusa and they told me to measure my X axis cantilever arm height on the right and left side. Left side was 12mm and right side was 10mm. You have to adjust the idler screws on the end of the arm to level it. Once I leveled it out the mesh bed leveling test performed all 16 test points and my first layer calibration went perfectly. No where in the directions does it tell you to adjust the idlers to level the bed. If it does I sure missed it and I just went through the directions again. Missed it twice if it is in there.
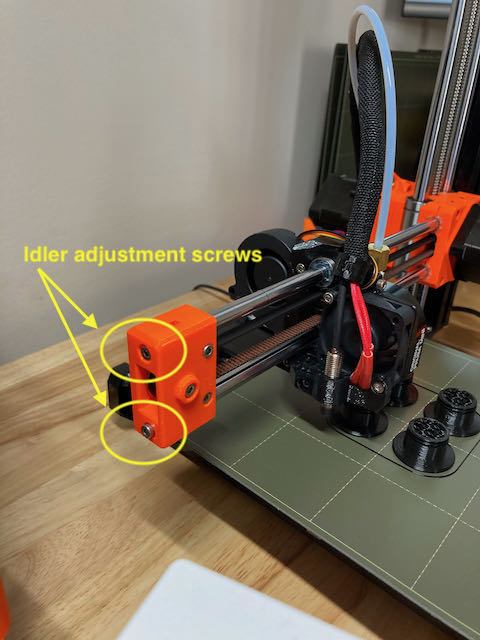
Idler screw adjustment
The funny thing about First Layer Calibration on all Prusa printers is that they have you just touch the print nozzle to the heat bed and then put a zip tie under the Pinda Probe to set the height. Then when you cal you have to spin the dial on the controller A LOT to bring the print head down to where the filament touches and sticks to the bed. The settings range from 0 -2 with my settings usually being around 1.3 to 1.6 which is a hell of a lot of spinning of the dial.
I always wondered why they don’t have you set the probe a little higher to make less of an adjustment and then it occurs to me that if I was them I would want newbie users to have the print nozzle up high and then ease it down to the surface, rather than get the probe too high and have the nozzle slam into the print bed. So for all of you who complain about the higher numbers on the First Layer Calibration…………..live with it 😀
There is one other thing that immediately caught my attention. The extruder clicks when it retracts. On Bowden extruders it is common to retract the filament during print head moves and lifts. That keeps material from oozing all over the place. It pulls it back just enough to keep things clean. On the Mini, this setting seems to be 3.2mm with a retraction speed of 70 and a Z lift of 0.2mm (these are default settings in Prusa Slicer, which of course you can change if you see fit).
Anyway……here is the clicking.
[kad_youtube url=”https://youtu.be/YPMyvrJyJPE” ]
I’ve never heard an extruder click like that. I have a compact Bowden on a REPRAP printer which I have used for years and it doesn’t click. If you go to the Forums there is quite a discussion about it, so right away I know it just isn’t me. It plain drives some folks crazy. I took the extruder apart and inspected it and best I can tell……..this is just the way it is. When the gears reverse, they click.
I confirmed this by doing Support chat again and they told me this was a normal noise and you could mitigate it by ensuring the motor gear was tight and to put one tiny dab of lube on the pulley gear. Sure enough that dropped the sound down some but it does still click.
This might make you crazy but I’ve already tuned it out. Knowing Prusa you can bet they’ll probably do an extruder upgrade or provide new STL’s for users to print. They DID NOT indicate this to me during chat but it just seems to be how they operate. My guess is that if enough people complain about it, that they will mitigate it in the future.
There are other extruders out there that are “upgrades” with the most popular being the Bondtech Extruder for the Prusa Mini. So I guess you can get rid of the click if you really want to. Changing extruders means playing around with the firmware and G code values though. Let me just say this. Bowden extruders use gears to push filament. The gears, the cleanliness of the gears, the tension on the idler, the QUALITY OF YOUR FILAMENT all seek to conspire against you to get a good even push to the print head. At some point the teeth will get clogged with ground filament and you’ll have issues. It happens. I’m sticking with the stock extruder which is EASY TO DISASSEMBLE and do maintenance on.
This is another reason I like to BUILD THE KITS. I see how it is built and I can see exactly how it operates and what it takes to perform simple maintenance.
So that’s that. My conclusions are that this is a LOT of printer at not a lot of cost. The improvements are substantial which tells me the next generation of printers is going to be even more amazing once they incorporate all this stuff into the line. The Mini+ would be a remarkable addition as a 2nd printer or a great 1st printer for someone getting their feet wet in the hobby. The only thing that scares me about that is that Bowden extruders are a different beast and once you jam one up or get a clog it is a mother to clear which can include disassembly of the print head. Not exactly newbie turf. Once you’ve done it a time or two, and it is inevitable that it will happen, it’s not that difficult to do.
I HIGHLY recommend this printer. Highly.
Here’s a shakedown video I did after my initial build.
[kad_youtube url=”https://youtu.be/rgv6exI-rhA” ]
And here is a time lapse I did with my GoPro!
[kad_youtube url=”https://youtu.be/_xa-olMTS2I” ]
Happy Printing!
Interesting review, just about to buy a mini+.
Had a refurbished ender 3 V2 before, but it had so many issues, had to send it back, decided that I like 3d printing, but don’t need the bigger volume of the ender.. so why not go up a level in quality..
Not saying the ender was bad, I think the refurb I got hadn’t been properly tested.
Just about to buy, and was looking at an refurbished Ender 3 V2 as well… happy I decided that I’m gonna take the step up