I bought a small CNC in maybe December of 2021, and in a month or so later I bought a proper CNC machine. Basically, I knew nothing about woodworking or CNC operations. But I taught myself. One small lesson at a time. Since I’m retired and in no hurry I decided to tackle skills one at a time.
So here I am just a few months later and while there is still lots to learn………….I’m cranking out beautiful pieces of woodworking. A couple of which have impressed my own self.
Probably the first Maker Machine I ever bought was a vinyl sign machine. I learned quickly that it isn’t only the ability to successfully make something it also includes the ability to NOT WASTE MATERIAL. Maximizing your stock is vital in becoming a skilled artisan. Here’s the most recent things that I made, and I have to say, to me, it is beautiful
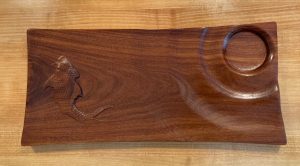
CNC Sushi Tray
It actually is a simple make. There are two bits used and three operations.
First a 1/4″ Upcut bit is used to rough clear the material.
Then it is followed up by a tiny 1/16″ bit that carves the details.
Then finally you put the 1/4″ bit back in to do a profile cut around the outside of the tray. Do some sanding and then oiling and you are left with basically a piece of artwork.
Continue reading