WHAT MAKES THE BEST LASER ENGRAVER?
The answer to that question can only be determined by examining how you intend to use your laser engraver. I’ll try to cover a few things in this blog that most people don’t think about before buying a laser. Here are some ways that a laser engraver can be used:
- For a Stay At Home business
- For a mobile business as a vendor at local festivals or flea markets
- As strictly a hobby device
- As a tool at your workplace
- As a way to supplement another machine such as a CNC (i.e. applying Makers Marks, logos, etc.)
If you decide that you are a Stay At Home user you can likely buy a larger, sturdier machine where speed may not be the most important requirement. Conversely, if you use your laser engraver as a mobile device you may desire a smaller, lighter, and more portable machine. The ability to make items quickly while customers wait could also be an important consideration.
If your machine is to be used for business you need to determine a strategy to reduce downtime.
I belong to several laser forums. Not a single day goes by that you don’t see a frantic call for help. “My machine is broken and I HAVE ORDERS TO FULFILL.” Don’t believe me? Just join a laser forum and see for yourself. It gets especially crazy in the months of November and December when people are most likely to buy Holiday themed items. I discuss this in greater detail here.
Staying operational with YOUR best choice for a laser engraver boils down to these two choices:
- Buy a machine that has spare parts available for purchase.
- Buy two (or more) machines.
LET’S EXAMINE THOSE CHOICES
Earlier Model Laser With Spare Parts Available (not recommended)
For some reason the latest generation of offerings do not offer a whole suite of spare parts available for purchase. Almost no new desktop diode laser engraver has a motherboard available for sale. I’d be willing to bet supply chain issues and worldwide chip shortages have something to do with that.
Recently I have seen posts from people who had failed Ortur motherboards who were told they will replace them when they receive stock. They don’t even have current sufficient levels of stock to service warranty claims. Yet they are still selling brand new lasers. Hmmmmm.
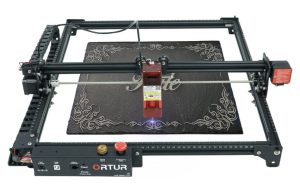
Ortur Laser Master Pro 2 S2
In order to buy an inexpensive laser and maintain some critical spare parts you literally have to jump back one generation of product evolution. If I were operating on a razor thin budget and could only afford one machine that had spare parts that are actually available then I would possibly consider getting an Ortur Laser Master 2 Pro S2. Motherboards are available at 3rd party sites such as Aliexpress. Other parts are also available.
Having a spare motherboard, laser head, and maybe some spare cables might end up costing you as much as buying a complete second machine though.
Buy Two Machines (recommended)
Again, every single day you will see that cry for help. “I have orders that must be made today and my machine is broken”. This is a 100% admission that you cannot afford to be non-operational, even for a little while. You need a back up machine. Your available strategies here are:
- Buy two new state of the art machines.
- Buy one new state of the art machine, and one older generation machine.
Obviously #2 is the more economical choice. Checking on Facebook Marketplace, eBay, and places that sell returned or refurbished lasers may be a good source of finding a gently used laser engraver.
What Laser Engraver Should I Buy?
For this section I’ll focus singularly on Desktop Diode Lasers since this is the entry point for the first time laser purchaser.
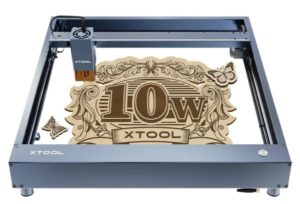
xTool D1 Pro
Everyone has a preference, and my choice of machine(s) is from xTool. xTool is head and shoulders above the competition in areas such a product development and innovation.
I personally own two xTool D1 Pro laser engravers, (10 watt, and 20 watt with extended bed). Having two machines is my personal strategy for maintaining 100% uptime. Actually I currently own 4 lasers, but who’s counting?
xTool has the highest power diode laser (20 watt) available. They also have a 1064 nm Infrared laser module for marking metals, and they just released a Fire Suppression System. No other company is even close in innovation at this point.
I have seen a couple laser companies gain some traction lately such as AtomStack or Atezr. I personally think AtomStack is not ready for Prime Time and I really have no experience with Atezr . Their web page doesn’t indicate any product timeline. They may be great machines but personally I’ll wait until they gain a lot more traction and indicate that they practice good Customer Service.
CUSTOMER SERVICE
When doing deep dive research on these machines you’ll frequently encounter the following complaints:
- Due to time differences between the US and China support emails and responses will take a day or two.
- Lengthy shipping times.
- Inability to speak to a human on the phone.
- Web based chats are robots only.
I read this the other day, and I’m paraphrasing here…….“My lens is cracked! I emailed them a picture and they answered me in the middle of the night. They didn’t answer my response today either. I should have bought a competitors product”.
Bad news, Sir. Every competitor is based in China and they all maintain the same Support hours.
There is one notable exception in the world of laser customer service though. xTool has a customer service rep on the Forum WHO WILL CONTACT YOU off line if you post an issue. Not 100% of issues I’m sure because she is just one person with probably other responsibilities. I posted an observation of some weird behavior. It would be a stretch to call it a problem. It was just me telling others, “Watch this”. I was contacted offline by the xTool Rep who engaged me in the issue and forwarded it to Engineering. Very impressive.
On the flip side of that equation I recently contacted Ortur Support via chat. I asked a question about replacement protective lenses and was told they would only replace one if it was broken and you proved it by sending a picture. And then they would only do that during the warranty period. There are NUMEROUS reports of those protective lenses cracking. That’s mighty poor support if you ask me.
LEARNING CURVE
If you have never assembled a 3 axis machine, and you have never USED a 3 axis machine it sort of stands to reason that you aren’t going to tear open the box and start making money. Once again, everyday on forums you will see these type of posts: “What are the settings for this kind of wood? I have orders to fulfill and I just don’t understand this machine at all.”
Say what? You dropped nearly a thousand dollars on a machine and you have no experience and you are already taking orders? Special emphasis should be placed on maintenance as well. If your strategy is to use the machine until failure then I guarantee you will succeed quicker than you planned.
RESEARCH BEFORE BUYING
Most people look at one thing. The cost of one unit. Consideration should be given to the following.
- Cost and availability
- Cost and availability of spare parts
- Cost and availability of accessories
- Customer Support
- Shipping Response Times
- COMMUNITY – Some companies have community pages with additional information and some have nothing.
- Reports of product failures
- Resolution of product failures
Before you buy you should read reviews of the machines online. Watch videos on YouTube. Read Amazon reviews, and join product Facebook forums and lurk and read the stories and most importantly, the resolution of those stories.
Read between the lines as well. Did the unhappy, furious customer cause their own problem? I read an unhappy furious customer story the other day regarding a cracked lens. In the picture they posted it was so painfully obvious that they dropped the laser head that it wasn’t even funny.
Play detective. Try to figure out who is being compensated for their review and whether that affects their review or not. I was provided an xTool machine for review and they quite literally told me to use it and write what I thought. Absolutely no pressure or no dangling carrot on a stick was offered up.
I liked that machine so much that I BOUGHT ANOTHER ONE WITH MY OWN MONEY. Conversely, I bought a new Ortur with my own money and have had problems that I should not have experienced. Support was less than helpful. Lenses are cracking all over the place on their new machines and they seemingly aren’t doing anything about it except sending you a warranty replacement. What that means is your machine is down hard until you receive the part from China.
I’m sorry. I like the machine and I’ll use it to apply my Makers Mark in my wood shop but I will NOT use as anything but a last resort for my laser based income. Just because I don’t like Ortur doesn’t mean that you have to. But I know what my needs are, just as you know what your needs are.
CONCLUSION
Don’t wake up one day and decide to become a laser millionaire and buy the first machine that you read about. Do serious research. Most importantly decide what it is you are going to make, and what your business strategy is. Tailor your purchase to what you intend to do with it. Not what that fancy laser expert on YouTube does with his or hers.